Nové materiály / Ľahké materiály / Kompozity s horčíkovou matricou /
Carbon fiber reinforced magnesium composite
(The material has been developed under a project No.: 4000117031/16/NL/NDe funded in the ESA PECS programme)
The combination of Mg and C fibres form one of the lightest structural materials in the world, with excellent strength and stiffness to weight ratio, good machinability, damping, heat conductivity and dimensional stability. Stable carbides at the fibre matrix interface do not impair corrosion resistance and support the long-term durability of material.
The elements forming stable carbides (Zr, Cr, Ti, Y) were used for alloying of Mg matrix. The Mg matrix - carbon fibre composites were then prepared by gas pressure infiltration (GPI) of molten matrix into the array of carbon fibres. The technology was develop to improve quality of fibre/matrix interface, whereas alloying elements were entirely spent for carbide forming reaction without any impact on Mg matrix properties.
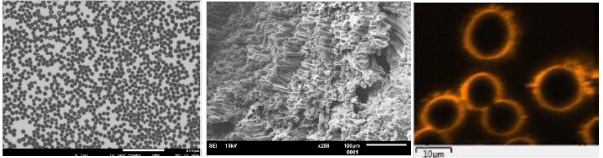
Microstructure of developed MgZr-C fibre composite (a – light microscopy, b SEM fracture surface, c – ZrC interface between fibre and matrix)
The prepared composites underwent detailed microstructural investigations and systematic testing of most important properties including corrosion test. The most promising composites achieved bending strength over 600 MPa and Young’s modulus over 300 GPa at the density of 1,8 g/cm
3.
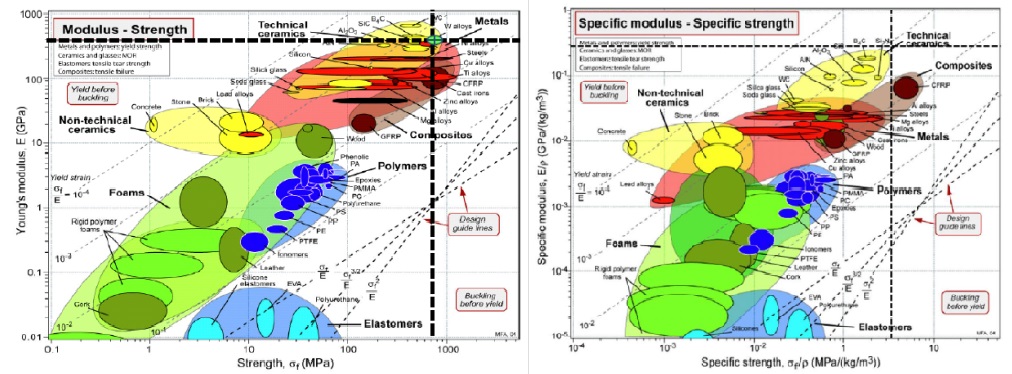
Mechanical properties of Mg1.8Y +50 vol.% Granoc fibre composites in comparison with other structural materials. (developed material is illustrated by dotted lines in Granta Design CES charts; best performance materials are located towards upper right corner)
The GPI technology makes possible manufacturing of complex shape components for many structural applications where high strength and stiffness at low weight is required. Nevertheless the anisotropy of the properties (different in the orientation parallel and transversal to fibre alignment) needs to be considered. Potential application fields are in aircraft construction (frame structures), lightweight robot arms, sporting articles, bicycle frames, etc.
The application potential has been demonstrated on cantilever demonstrator that has been compares with its counterpart made of conventional Mg alloy. The both components of the same shape and dimensions possessed similar weight of 65 g. The higher self-frequencies obtained for demonstrator made from the composite confirmed significantly higher stiffness of composite in comparison with cast Mg part. The composite exhibited also good damping represented by loss factors of η = 0.002 that was one order of magnitude higher than those obtained for Mg component (η = 0.0008). Bending test confirmed that the stiffness of the component made of composite was much higher (Young modulus of 258 GPa) than the stiffness of cast Mg part (Young modulus of 46 GPa). The ultimate bending force obtained for composite was also 3 times higher than the one obtained for cast Mg component